Porosity in Welding: Identifying Common Issues and Implementing Ideal Practices for Avoidance
Porosity in welding is a prevalent concern that frequently goes undetected until it triggers considerable troubles with the integrity of welds. This usual issue can endanger the strength and durability of welded structures, positioning safety and security threats and resulting in costly rework. By comprehending the source of porosity and executing effective avoidance strategies, welders can significantly enhance the top quality and integrity of their welds. In this discussion, we will explore the vital aspects contributing to porosity formation, analyze its harmful effects on weld performance, and go over the best practices that can be adopted to lessen porosity incident in welding procedures.
Typical Root Causes Of Porosity
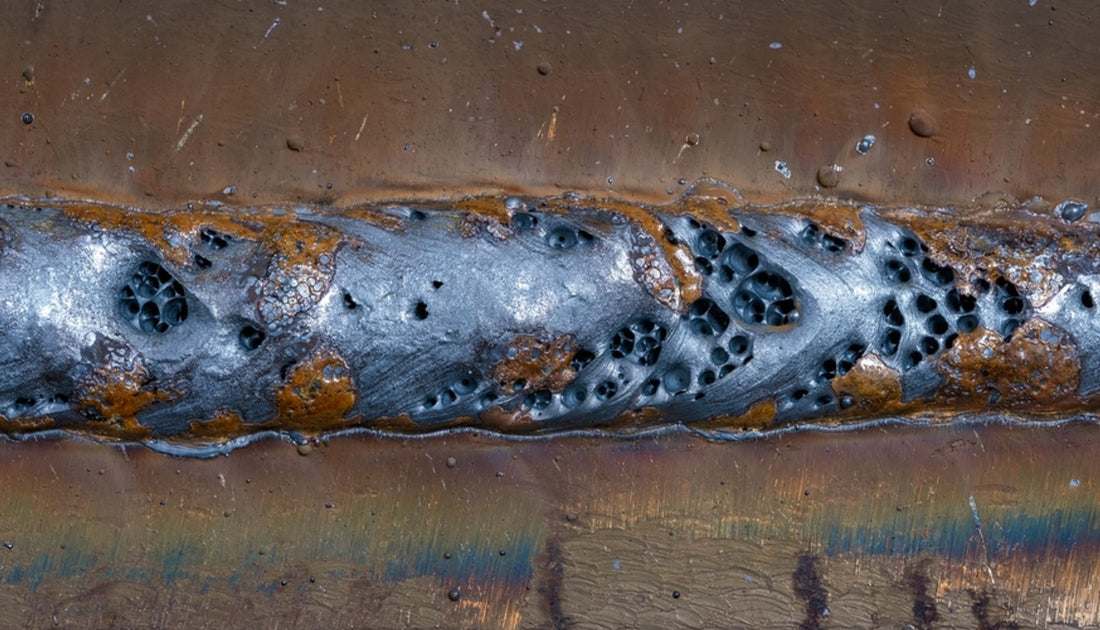
Using unclean or wet filler materials can present impurities right into the weld, adding to porosity concerns. To reduce these usual reasons of porosity, thorough cleaning of base metals, proper protecting gas choice, and adherence to optimal welding parameters are important methods in accomplishing top quality, porosity-free welds.
Impact of Porosity on Weld Quality

The visibility of porosity in welding can dramatically jeopardize the architectural stability and mechanical residential properties of welded joints. Porosity develops gaps within the weld steel, weakening its general toughness and load-bearing ability. These gaps work as tension focus factors, making the weld much more susceptible to fracturing and failing under applied loads. Furthermore, porosity can minimize the weld's resistance to deterioration and various other environmental elements, better decreasing its longevity and efficiency.
Welds with high porosity levels tend to display lower impact strength pop over to these guys and lowered capacity to warp plastically prior to fracturing. Porosity can impede the weld's capability to successfully send forces, leading to premature weld failure and possible safety risks in important structures.
Ideal Practices for Porosity Avoidance
To improve the architectural honesty and quality of welded joints, what particular actions can be carried out to lessen the event of porosity during the welding procedure? Using the right welding strategy for the certain product being welded, such as readjusting the welding angle and weapon placement, can better avoid porosity. Routine evaluation of welds and immediate removal of any kind of problems identified throughout the welding procedure are important practices to stop porosity and produce top notch welds.
Relevance of Proper Welding Techniques
Executing proper welding techniques is paramount in ensuring the architectural stability and top quality of bonded joints, constructing upon the structure of reliable porosity avoidance steps. Excessive warmth can lead to raised porosity due to the entrapment of learn this here now gases in the weld pool. In addition, making use of the ideal welding criteria, such as voltage, present, and travel speed, is crucial for attaining sound welds with minimal porosity.
Additionally, the selection of welding process, whether it be MIG, TIG, or stick welding, ought to align with the particular needs of the task to make certain optimal results. Proper cleansing and preparation of the base metal, as well as picking the appropriate filler product, are likewise crucial elements of skilled welding techniques. By adhering to these best methods, welders can reduce the danger of porosity development and produce high-grade, structurally sound welds.

Evaluating and Quality Control Actions
Quality assurance measures play a vital duty in confirming the integrity and dependability of bonded joints. Testing treatments are vital to find and prevent porosity in welding, making sure the strength and resilience of the end product. Non-destructive screening techniques such as ultrasonic Get the facts testing, radiographic testing, and aesthetic inspection are frequently utilized to determine potential flaws like porosity. These techniques permit for the assessment of weld high quality without compromising the stability of the joint. What is Porosity.
Post-weld inspections, on the other hand, assess the last weld for any issues, consisting of porosity, and verify that it meets specified standards. Carrying out a comprehensive high quality control strategy that includes complete testing procedures and assessments is paramount to lowering porosity problems and guaranteeing the total quality of welded joints.
Verdict
In conclusion, porosity in welding can be a typical issue that influences the top quality of welds. By recognizing the typical reasons of porosity and applying finest techniques for avoidance, such as proper welding strategies and testing actions, welders can guarantee excellent quality and reliable welds. It is important to prioritize avoidance techniques to reduce the event of porosity and keep the stability of welded structures.
Comments on “Specialist Guidance on What is Porosity in Welding and Exactly How to Resolve It”